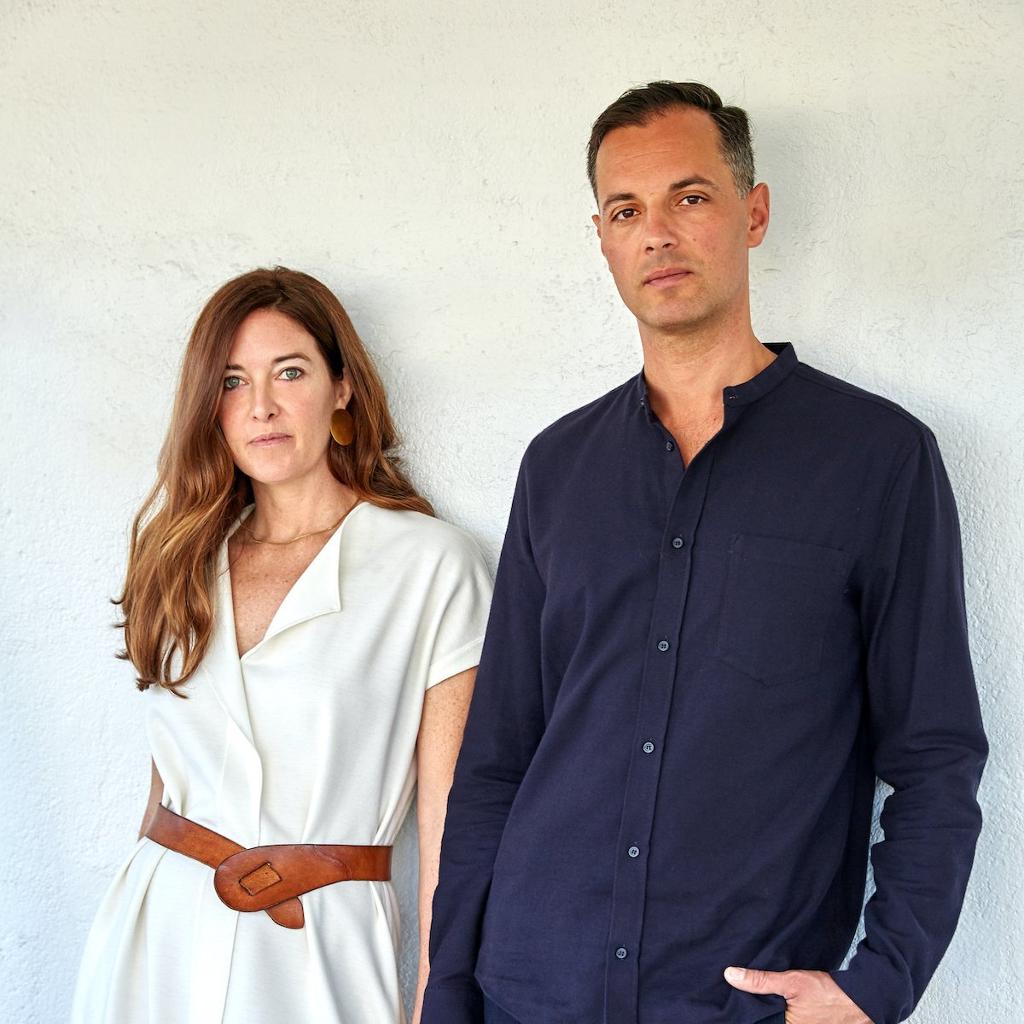
Sustainability, California Style – A Brief Look into the World of Kalon Studios
Michaele Simmering and Johannes Pauwen are the wife-and-husband duo behind Los Angeles based furniture studio Kalon. Together, they have crafted a unique take on the California Style of interior design that perfectly balances aesthetic, production and logistical cleanliness to deliver a range of stunning and sustainable interior products. Riluxa spoke to Michaele about her influences and her exacting ethical standards.
Natural materials form the basis of almost all your work. To you, personally, what was the initial appeal of wood and what were some of the first pieces you remember connecting with that inspired you to work with it?
Wood is so pervasive I can’t honestly say I remember the first connection. There are boats in childhood, creaking floors, kitchen tables, burnt candlesticks, dented cabinets with deep patinas. Wood has a life to it. It absorbs human contact in a fascinating way. What I respond to most is the inherent variations that you can’t control for; they stand in opposition to the precise form that we, as designers, bring to a piece. The two intermingle in a way that interests me. They enhance one another.
Rugosa Collection - Bookshelf, Coffee Table and Chair
Do you think, as consumers, there’s a connection between our aesthetic appreciation of timber furniture and our ability to trace it back to its source and the people who crafted it?
I think we’re getting better at it. As consumers, we’ve been trained to be blind to the human activity behind the production of a piece. Everything is readily available everywhere. It doesn’t matter where we live, big city or deep woods, we’ve gotten used to the idea that we can have something overnighted to us. When we think like this, when we’re dealing with immediate gratification, there is no appreciation for process. Lead-times are seen as delays and therefore irritants. One of the things we’ve worked hardest on since founding Kalon is to better educate our customer base about our process, so that they understand that the delay between purchase and delivery isn’t a vacuum. It’s time spent by many hands making them the piece. In the same way, we strive to educate them about the beauty of variation, the moments we can’t control for in material and hand-craft. These variations have great value and we want them to be perceived as such. Let’s be honest, we could approach how we build and sell things very differently. We could focus on sales and margins and warehousing to close the gap, but we don’t. We are making each piece at a time when craftspeople are increasingly rare, from very particular materials, to a very high quality, and that’s all deliberate. I think anyone buying our pieces at this point is aware of those choices and they value them.
Here in the 21st Century, we are seeing a return to traditional techniques to deliver the aesthetics of industrial Minimalism. Do you feel like cultural perceptions of beauty have been forever changed by 20th Century factory production methods?
Nothing is forever but yes, the Bauhaus changed everything. I don’t see beauty as finite or materially definable. For humans, all things have an ideal. The closer the realization of a given object to its ideal, the more beautiful it is. Industrial minimalism is one expression of beauty. In the 20th century, there have been a lot of movements that have reacted against industrial minimalism. For example, there’s Memphis, Droog, and here in LA we have the Haas brothers who are the antithesis of industrial minimalism. Right now, we are seeing a trend towards maximalism. All of these movement are reactions to the Bauhaus and the international style - and so are born from it - but they present varied interpretations of beauty.
Another facet of what you’re talking about is perceptions of beauty as they pertain to craft. I do think that in the post war period there was a movement away from anything handmade. There was an obsession with the new and shiny. Uniformity and automation were highly valued. There was a fascination with the future and the concept of progress. Human culture was seen as hurtling towards a Jetson like future. This continued to play out through the 80s and 90s. Around the turn of the century, as American culture started questioning the value of box stores, mass production, mono cropping and big agriculture, boutique culture found value, and the maker movement was born. This happened alongside a surge of interest in farmers markets, farm-to-table restaurant culture, seasonal produce, etc. I don’t think we’ve lost our interest in the perfection of plastics, as you can see with mass market goods like cell phones, but I do think we’ve seen a rise of interest in the beauty of imperfection and handcraft. Not to equate handcraft with imperfection, but the inherent small variations that come from handcraft, even at a level of expertise, now rightly have a perceived value.
How you do define craft as it pertains to Kalon products?
For me, craft is quality and expertise. Above all else, it’s mastery of technique. A lot of the time, the word craft evokes tradition for people. We imagine old hands whittling or forging with generations of knowhow. There is a reality to this - some of the best craftspeople we work with come from families who have been doing the work for generations - but craft equally applies to state of the art processes. So it’s about approach and knowledge and not about traditional tools. The craftsperson’s job isn’t to simply build the piece. It’s to realize each design to the highest standard.
You spent some years living and working in Berlin. How did it affect your outlook on product design and how important has it been in terms of developing your business at the international level?
From the outset, Kalon was intended to be an international company with production and distribution in both the US and Europe. This intent was a direct outgrowth of our time living in Berlin. Johann, my partner is German. We have a life in Germany, and Kalon reflects that.
We lived in Berlin in the early 2000s. Culturally, the city was incredibly rich but economically it was depressed. There weren’t many opportunities. As a result, we learned to be organized and diligent. Nothing was wasted. Life was very DIY and the aesthetic in Berlin mirrored that. Everything was made from conventional materials. Construction was lean. Our first collection of work pulled heavily from the Berlin aesthetic. We worked with sheet material. More broadly, I’d say the impact of those years is seen in our approach to design and production which is fairly European.
Caravan Nursery Collection - Crib
What part do digital technological advancements play in allowing a business like yours to be more environmentally conscious?
We are very much a business shaped by the digital world we live in. We have leveraged it to its fullest extent to build Kalon. This spans from how we develop and distribute our collections to how we communicate with our vendors and customers. When we design and develop a piece, it is done digitally, using CAD software. We almost never require revisions or build physical prototypes. This also allows us to build in incredible efficiencies in the production process so that there is no waste. Our factories employ digital wood dimensioning tools to further reduce wood waste. We also seek out factories who are at the forefront of industrial development and who employ batch size-one production flows. This means that producing a single piece is as efficient as producing large production runs, which has a domino effect - less warehousing, less transport, less heating and overall less waste by not producing goods that aren’t needed.
How about during the coronavirus crisis? How important has digital interconnectivity been in terms of maintaining an industrial ecosphere? Have you provided a blueprint for the new norm?
I think our business model and approach were uniquely situated for this moment. Amazingly, we saw almost no interruption in production and sales, which we feel so grateful for, and has deepened our commitment to a 360 approach to running a sustainable business.
Kalon was initially set up to be run with two cell phones and two laptops. In a sense this setup has never changed. We outsource manufacturing. We keep a small staff and run our office out of our home. This has served us well as it has allowed us to be dynamic and able to adapt to new situations very quickly - to scale up or to scale down almost instantaneously. Although it means we pay a little more to produce the product, it has allowed us to run an incredibly lean operation and focus on design and process. Producing in the US or 'locally' has also been a good decision. We don't have to deal with importing large volumes of inventory to warehouse and ship. We are able to produce on demand, to ship direct, etc all while greatly reducing our carbon footprint. Because of this structure we've been able to survive crises that have sunk many of our peers and competitors - like the 2008 financial crisis and now the pandemic.
The COVID crisis has brought incredible clarity to a lot of complicated structures. For example, it has made it clear how much domestic supply chains matter. It's also laid bare the incredible inequities between the invested class and the working class. Kalon's road has been long and filled with its fair share of setbacks and hardships but we have never lost the founding principles of equitable fair business practices that sustain both us and the tradespeople we work with. It's a mutually beneficial relationship that provides a solid income, security and pride in work for all of the people involved in the production process. Exactly right now, we are reminded of how much that matters and I think it's something that a lot of people value in the midst of the pandemic – and hopefully will for years to come.
To find out more about Kalon Studios, visit their website.
Looking for something else to read? Check out our interview with RIBA Award-winning architect William Smalley.